

If you want to control the speed of rotation of a simple DC Motor, then there is a technique called PWM DC Motor Control. reverse the polarity, the motor will rotate in reverse direction. It is very simple to operate: connect the two leads of the motor to the two terminals of a battery and voila! Your motor starts rotating. There is technically no right or wrong way.A DC Motor is the simplest of motors that beginners and hobbyists encounter. You can swap out your motor’s connections. Note that both Arduino output pins 9 and 3 are PWM-enabled.įinally, wire one motor to terminal A (OUT1 and OUT2) and the other to terminal B (OUT3 and OUT4). Now connect the L298N module’s Input and Enable pins (ENA, IN1, IN2, IN3, IN4 and ENB) to the six Arduino digital output pins (9, 8, 7, 5, 4 and 3). We’ll use the on-board 5V regulator to draw 5V from the motor power supply, so keep the 5V-EN jumper in place. Next, we need to supply 5V to the logic circuitry of the L298N. Because L298N has a voltage drop of about 2V, the motors will receive 10V and spin at a slightly lower RPM. We will therefore connect an external 12V power source to the VS terminal.

In our experiment, we are using DC gearbox motors, also called “TT” motors, which are often found in two-wheel-drive robots. Let’s begin by connecting the motor power supply. Now that we know everything about the module, we can start hooking it up to our Arduino!
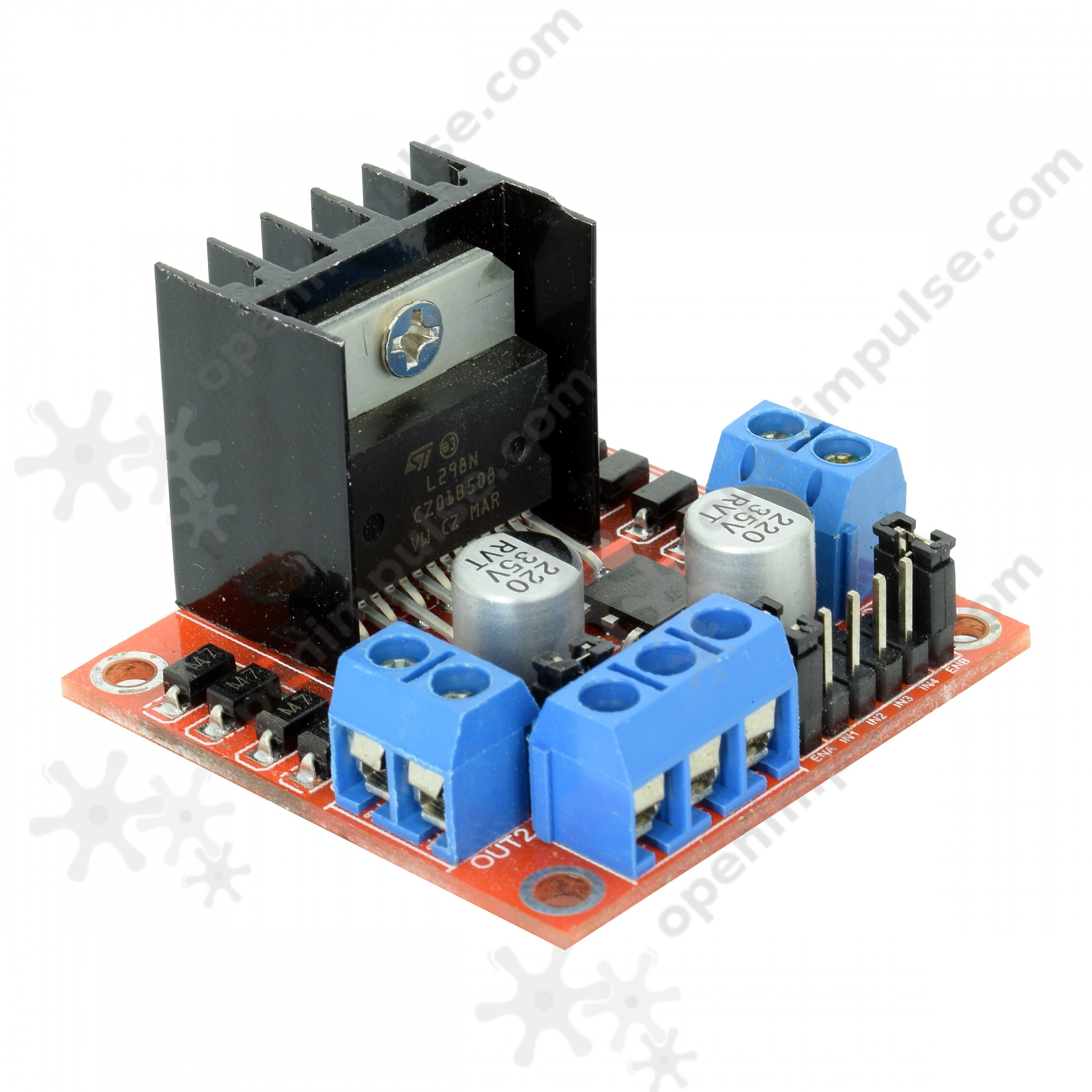
Wiring an L298N Motor Driver Module to an Arduino This is why the L298N based motor drivers require a big heatsink. This excess voltage drop results in significant power dissipation in the form of heat. The image below shows PWM technique with various duty cycles and average voltages. The shorter the duty cycle, the lower the average voltage applied to the DC motor, resulting in a decrease in motor speed. The higher the duty cycle, the higher the average voltage applied to the DC motor, resulting in an increase in motor speed. This average voltage is proportional to the width of the pulses, which is referred to as the Duty Cycle. PWM is a technique in which the average value of the input voltage is adjusted by sending a series of ON-OFF pulses. A widely used technique to accomplish this is Pulse Width Modulation (PWM). The speed of a DC motor can be controlled by changing its input voltage.
